- NASA - Spin Forming.
- What is Sheet Metal Spinning or Spin Forming? - Knords Learning.
- Spinning process - SlideShare.
- Flexible Spinning Forming Technology | SpringerLink.
- A review of spinning, shear forming and flow forming processes.
- The Ultimate Guide to Metal Spinning With Diagrams.
- Flow Forming - A Complete Overview - Advanced Structural.
- Metal Spinning Technology | MetalForming Magazine Article.
- CN114226586A - Butterfly-shaped end socket spinning forming process.
- Spinning process optimization and microstructure of stainless-steel.
- Hot Spinning | PMF Industries, Inc.
- Hot Working: Definition, Methods, Working Process, Advantages.
- Spinning Process Overview: From Fiber Material to Yarn.
- Handbook: The Ultimate Guide To Metal Spinning - wordpress.
NASA - Spin Forming.
Publication Publication Date Title. GB1309969A 1973-03-14 Process and apparatus for continuous extrusion of highly viscous melt. EP2416100B1 2017-09-20 Hopper structure for a dehumidification plant and method for dehumidifying granular plastic material. GB938056A 1963-09-25 Melt spinning. When working with metal spinning, the flat metal forms over a male tool. This means no part can be smaller than the machined tool, and thus in circumstances of very tight tolerances we can work with a .060quot;/ gt; -.030quot;. Metal Spin Forming Thickness. During the metal spinning process, some amount of material thinning will occur.
What is Sheet Metal Spinning or Spin Forming? - Knords Learning.
In the first attempt, we recommend practicing metal forming a flat-bottomed cylinder, roughly 50.8mm in diameter and 76.2mm high. This will require a 127mm diameter disc and a mandrel commonly referred to as a #x27;chuck#x27; that you will form the disc over. You will also require a manual Metal Spinning Lathe that you will use to carry out the. Shear spinning involves forming the work over the mandrel, causing metal flow within the work. This metal flow will act to reduce the thickness of the work as it is formed. The initial diameter of the work can be smaller in shear spinning. Limits to the amount of reduction of work thickness exist in order to prevent fracture. Metal Spinning. Established in 1891, Leifeld has been a leading innovator in the field of metal forming technology and the result is today#x27;s state-of-the-art Playback/ CNC spinning machines. Skill-recording controls backed by CNC with graphical editing and programming features allow traditional craftsman#x27;s skills to be captured and.
Spinning process - SlideShare.
Therefore, this study simulates the spinning of 439 stainless steel welded pipes using ABAQUS software. ABAQUS is used to simulate spinning forming under different process parameters. The effect of the process parameters on spinning forming is studied to provide guidance and theoretical reference for practical spinning applications. Repeat. Hot spinning heats a flowformed metal tube as it spins on a lathe at high speeds while various rollers and tools shape the piece. Computers control various machine tools that adjust for everything from feed rate, coordination, location, temperature and speed. The process accurately controls the profile of the neck while delivering. Metal forming processes are used to apply stress, compression, or both upon a piece of metal. Metal forming may also be used to cut, drill, fold or bend the workpiece. This is done for plastic deformation, i.e., to geometrically change the metal piece to be used as a component or part in the next manufacturing step.
Flexible Spinning Forming Technology | SpringerLink.
This system based on developing a synchronous spinning machine, in which the rotational motion and feeding of the tradition lathe machine were measured and control to maintain the speed synchronization with the trajectory of the forming tool rollers a special tool of forming, where this tool controlled by the electrical motors. Flow forming FF is an incremental plastic deformation process permitting an axial elongation of a hot preformed part, defined as preform, mounted on a rotating mandrel, by means of a radial.
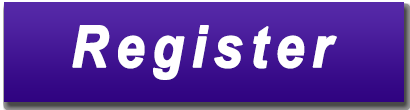
A review of spinning, shear forming and flow forming processes.
Additional Forming, Deep Drawing, Hydroforming, Stamping, Machining, Cutting,, Lubricants. Contact us for pricing: 719 282-9061. ILOFORM PS 700, ILOFORM PS 326, ILOFORM PS 364, PERFORMANCE BIO NC ULTRA LITE EP, PERFORMANCE BIO NC LITE, PERFORMANCE BIO NC SUPER LITE, Castrol Hysol MB 50, and more. tooling engineering amp; manufacturing. As shown in Fig. 1, the single pass deep-drawing spinning process with a flat sheet metal blank was adopted [ 15], where D r, r,and refer tothediameter,nose radius,and installation angle of roller, and h refers to the forming height during spinning. The blank material was cold rolled steel sheet SPCC with thickness t 0=2 mm. Three types of.
The Ultimate Guide to Metal Spinning With Diagrams.
Tube bending describes the process used to form metals and other types of materials into tubing or pipes. The processes by which metal tube bending takes place may involve a variety of methods using temperature, equipment, and materials. For the purpose of this resource, we are focusing on metal tube bending and forming.
Flow Forming - A Complete Overview - Advanced Structural.
. Metal Spinning Services Metal spinning, also known as spin forming, metal forming or metal turning is a cold work metal forming process which forms metals into axially symmetric parts. The process begins with flat sheet metal cut into a disk and is then formed over a rotating mandrel into a round shape.
Metal Spinning Technology | MetalForming Magazine Article.
The conical rotary part with variable wall thickness is a typical aircraft engine sheet metal casing, which requires high forming quality. In this paper, the hot power spinning process of conical rotary part with continuously variable wall thickness of superalloy GH4169 was simulated by DEFORM-3D FE finite element software. The equivalent stress, equivalent strain and temperature. Spinning is a process used to produce an axis-symmetric hollow shape by the application of lateral pressure from a forming tool, to a rapidly revolving circular blank of sheet material, causing it to assume the shape of a former that is rotating with it. This page was published over 5 years ago. In the situation the spinning process is very similar to deep drawing. The spinning process also enables... Metal forming process are classified into bulk forming processes and sheet metal forming processes.In both types of process, the surface of the deforming metal and tools in contact, and friction between them may have a major influences.
CN114226586A - Butterfly-shaped end socket spinning forming process.
. The spinning process is accomplished by the use of pressure against the rotating circle from a quot;spin toolquot; which may take the form of a roller mounted on a lever, a hand tool or a hydraulically powered roller which allows the forming of thicker or less formable alloys. The process, difficult to describe by text, is shown in the video below..
Spinning process optimization and microstructure of stainless-steel.
The stretch forming process is seldom suited to progressive or transfer operations. Although the process can create sharp contours and reentrant angles, it is best for forming shallow or nearly flat shapes. Stretch forming uses bulldozing or joggling as a secondary operation to draw form, or indent, parts during or after forming..
Hot Spinning | PMF Industries, Inc.
The design and control of a deep drawing process depends not only on the work piece material, but also on the condition at the tool work piece interface, the mechanics of plastic deformation and the equipment used. This project describes the use of ABAQUS finite element code in sheet metal forming simulation on circular cup deep drawing.
Hot Working: Definition, Methods, Working Process, Advantages.
Spinning Spinning, sometimes called spin forming, is a metal forming process used to form cylindrical parts by rotating a piece of sheet metal while forces are applied to one side. A sheet metal disc is rotated at high speeds while rollers press the sheet against a tool, called a mandrel, to form the shape of the desired part. The invention discloses a spinning forming process of an extra-high-voltage shielding cover. A computer digitally controlled spinning machine is adopted to integrally process a plate material into the extra-high-voltage shielding cover.
Spinning Process Overview: From Fiber Material to Yarn.
Blank thickness is nothing but thickness of blank.The process of metal spinning is capable of forming workpiece with thickness of 0.5 mm to 30mm. To obtain uniform thickness during a spinning it required high speed ratio but this will reduce the geometrical accuracy which applicable for shear spinning. STEPS IN SPINNING PROCESS Step 1 Metal Forming This step involves the laying down of the material onto the mandrel. It is accomplished with short inside to outside moves. Material gets easier to form as the part is closer to completion Step 2 Trimming Parts having been spun are trimmed at the end to blunt sharp edges and also to.
Handbook: The Ultimate Guide To Metal Spinning - wordpress.
Spinning than in press forming. Manual metal spinning and power spinning are generally in competition with pressing and deep drawing. Equipment for Manual SpinningLathes and Tooling. A simple tool and sheet preform setup for manual metal spinning is shown in Fig. 5a. The forming mandrel is mounted on the headstock of a lathe. The circular. In multi-pass conventional spinning, the design of roller path is a critical problem due to its sensitive effect on the deformation mode and forming defect during spinning process. However, at present, the roller path is still mainly designed based on experience and trial and error, which seriously restricts the high-performance spinning of TCPCS.